What are the possible scenarios that require autofocusing in industrial inspections?
Autofocusing is a valuable feature in industrial inspection applications where maintaining sharp focus on the object or scene is crucial for accurate analysis, measurement, and quality control. Here are some scenarios in industrial inspection where autofocusing is commonly required:
Variable Object Distances: Autofocus sharpens images regardless of varying object distances, eliminating the need for manual adjustment.
High-Throughput Environments: Autofocus maintains focus in fast-paced environments, optimizing image capture efficiency.
Precision Inspection: Autofocus ensures precise focus for detailed inspection tasks, reducing errors in analysis or quality control.
Remote Monitoring: Autofocus remotely adjusts focus settings for cameras in remote or inaccessible locations, simplifying maintenance and monitoring.
Lens Changes or Swapping: Autofocus streamlines lens changes, minimizing downtime and maintaining consistent image quality across different setups.
Common autofocusing challenges in industrial settings
For clear visibility of varied heights, opt for a larger depth of field (DoF) with a smaller aperture (bigger F number). However, this requires longer exposure for ample brightness. In high-speed applications, a wider aperture (smaller F number) is needed for sufficient light, but it limits depth of field, impacting focus.
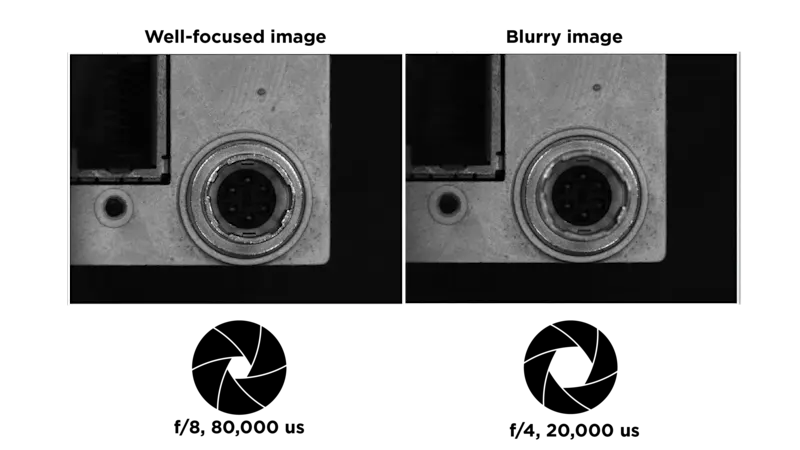
What are the different AF methods and their trade-offs?
In professional imaging, autofocus methods typically fall into two categories: active and passive. Both approaches are used in industrial applications, and they have their respective advantages and limitations. Next, we will look at them one by one.
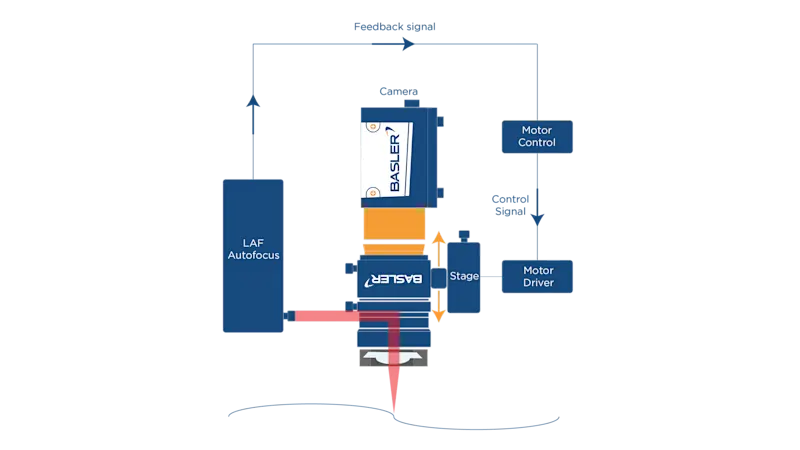
Active Autofocus
In an active autofocus system, a distance detection device is used to calculate the working distance; then the imaging system is positioned accordingly. The most common solution in industrial settings is a laser autofocus.
Laser AF solution proves beneficial when the working distance of the application cannot be predicted. Also, it excels in distance detection speed and accuracy.
However, the hardware setup is rather complex, leading to naturally higher costs. Another drawback is its low flexibility.
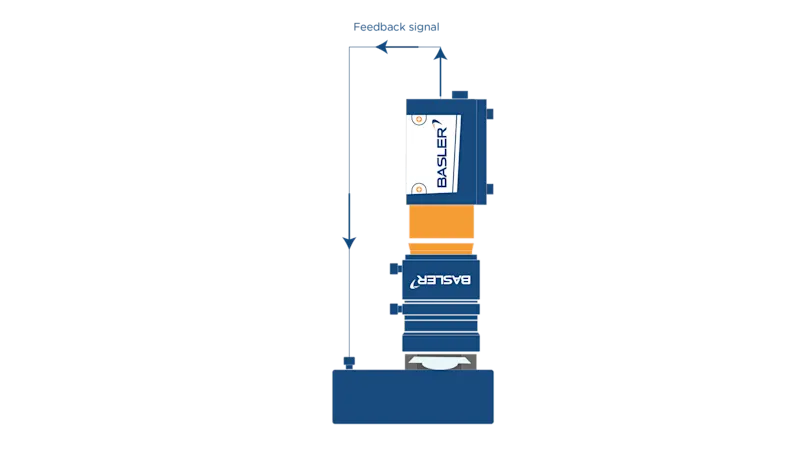
Passive Autofocus
The two passive autofocus methods are phase-detection autofocus (PDAF) and contrast detection autofocus (CDAF).
PDAF is typically integrated into consumer camera sensors but can be customized for larger industrial projects.
In a CDAF system, multiple images are captured as the working distance changes and the focused image is picked out through evaluation. Thanks to its simpler system architecture, lower costs, and greater flexibility, CDAF solution finds wider application in industrial scenarios. However, system integrator will need to develop programs to integrate focus lens and AF algorithms.
How to select and develop your own autofocus solution?
In engineering, there's typically no perfect solution that solves all problems at once. The suitability of an AF solution depends on your application requirements.
The following comparison chart provides a comprehensive overview of the advantages and limitations of different approaches for industrial autofocus. Four distinct autofocus methods are compared based on their re-focusing speed, result accuracy, system flexibility, complexity, and cost.
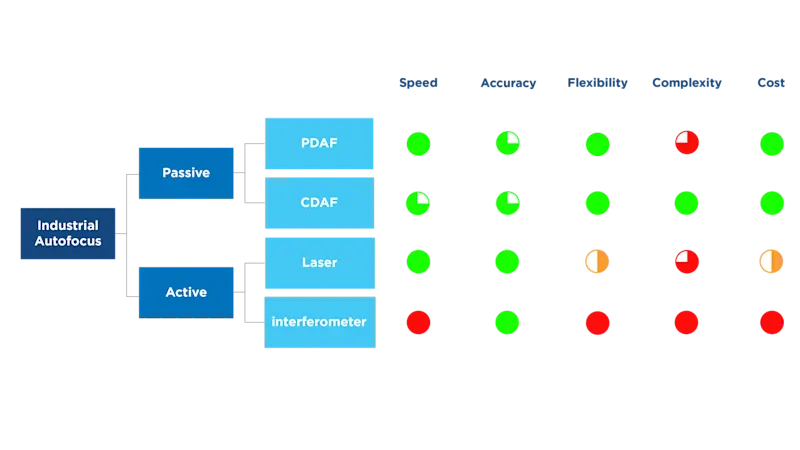
So, if your project requires higher accuracy, even with the associated higher cost and system complexity, a laser-based autofocus method is the optimal choice. If the speed and accuracy offered by CDAF solution already meet your project requirements, it stands out as the most cost-effective option that excels in all aspects. Do take the following aspects into consideration if you opt the CDAF approach:
Coordinating AF lens control with camera
Developing autofocus algorithms
Addressing CPU loading
What are the available CDAF solutions in the market?
Searching for top-notch Contrast Detection Autofocus (CDAF) solutions in the market? The following section depicts and compares different CDAF solutions, so that you can find out which one would be suitable for your specific project based on your project requirement and priority.
Evidently, Solution 3 stands out in both lower hardware cost and minimal software efforts. Solution 4 also provides a ready-for-use AF algorithm, but it's more suitable for high-end applications where frame grabber is required.
When faced with tight project deadlines or the complexities of assembling the perfect team to develop autofocus solutions independently, turning to professional vision solution providers is a strategic move.
Related topics
If you would like to watch live demonstrations of the autofocus solutions by Basler, go to our on-demand webinar. Entrust your project to the experts who understand your vision needs inside out. Read about a suite of cutting-edge solutions that promise precision, efficiency, and seamless integration.