Robot arm cameras
The Stereo visard camera for precise, smart image processing in dynamic environments
Cameras allow robots to perceive their surroundings, recognize objects, and perform complex tasks. In order to perform these tasks, robot arm cameras must be able to compensate for vibrations, process image data in real time, and offer seamless integration. This requires special cameras designed to overcome these challenges.
Typical applications for cameras mounted on robot arms
Thanks to its vibration resistance and compact design, the Stereo visard camera is ideal for industrial use on robot arms and in dynamic environments.
The on-arm assembly of industrial cameras enables compact and flexible robot cells. With the robot arm, the camera's shooting position can be freely varied. This allows objects to be viewed precisely from different directions and at close range.
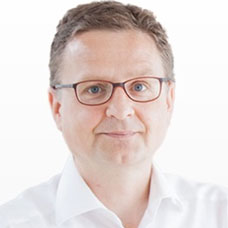
Our industrial-grade 3D stereo cameras for robotics applications
The camera for the best results on a robot arm
Although there are huge benefits to having a camera on a robotic arm, there are some challenges that need to be considered. The Stereo visard camera has been specially developed to meet these requirements.
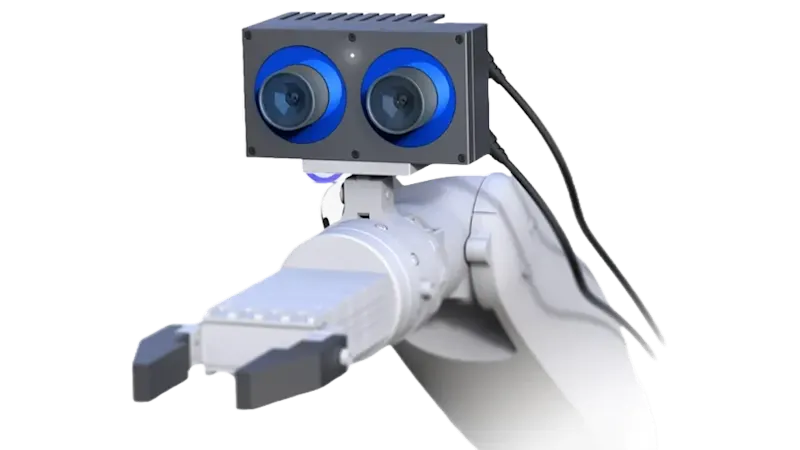
Defies vibrations, shocks, and splashes
Robotic arms generate vibrations that can lead to blurred images. Our Stereo visard camera convinces with sufficient mechanical stability to avoid these issues, and also takes into account the harsh conditions found in production environments:
Resistant to vibrations up to 5 g and shocks up to 50 g
M12 Connectors ensure secure cable connections
Splash-proof, thanks to IP54 Class
Real-time capability for reliable results
For many applications, especially with rapid movements of the robotic arm, it is crucial that image processing takes place in real time.
The Stereo visard camera offers Real-time data processing through On-Board Processing: Image data is processed directly on the camera, and the system can react quickly. An external computer is not required.
Collision avoidance thanks to Collision Check
Robotic arms often have to make do with limited space and perform fast movements in close succession. This can easily lead to collisions and, in the worst case, the camera can be decalibrated. Thanks to Collision Check, the Stereo visard works reliably, even in small spaces.
The Collision Check Function of the software modules 3D ItemPick, 3D BoxPick or 3D SilhouetteMatch prevents the gripper from colliding with other objects.

Easy integration into the robotics application
The integration of a camera system into the robot controller is essential, and a crucial factor for the efficiency and reliability of robotics applications.
With its Ethernet interface, The Basler Stereo visard camera ensures stable and fast data transmission and enables easy integration into existing systems.
Software interfaces available for a wide range of robotics brands, such as: ABB, FANUC, Franka Robotics, and Fruitcore Robotics. We provide KUKA, Techman Robot, Universal Robots, and Yaskawa Motoman Robotics software interfaces for camera control.
The integration of special gripping systems, such as Vacuum Gripper from LARD, are also covered by the software interfaces.
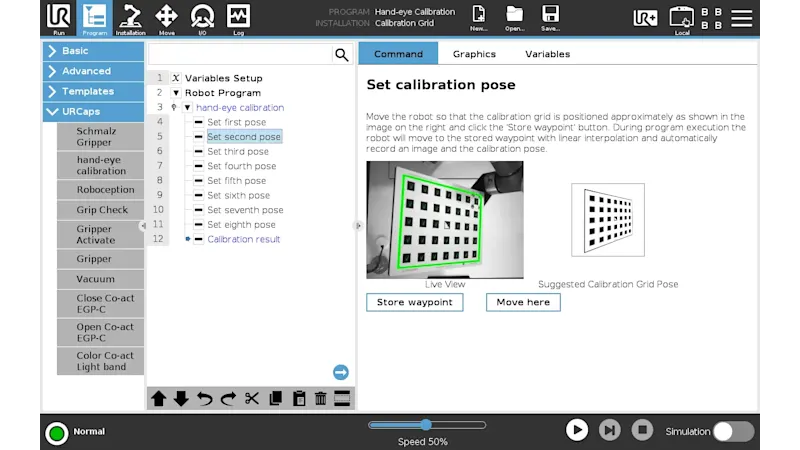
Precise calibration of the camera and robot arm
One Hand-eye calibration is required when a robotic system uses a camera to detect objects and then interacts with them using a gripper or tool. After all, the system must know how to translate the camera's coordinates into the robot's coordinates.
Simple: The Hand-eye calibration can be done manually via a web GUI or programmatically via the REST API interface .
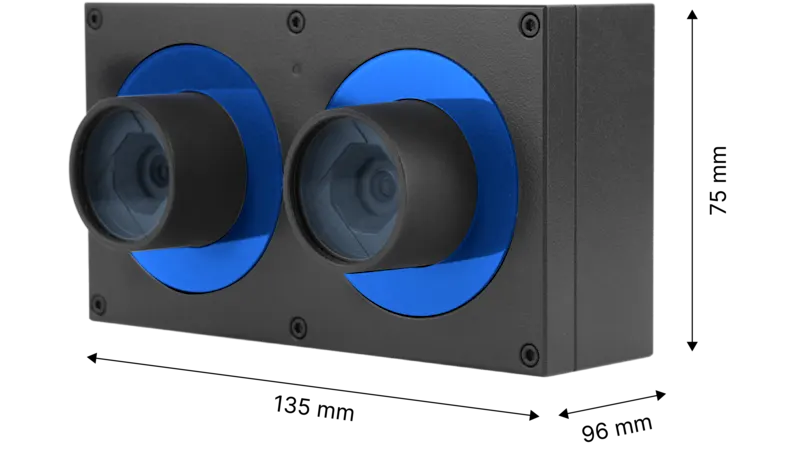
Lightweight and compact
Robotic arms have limited capacities in terms of the additional weight that can be accommodated.
Light: Low weight from 0.68 kg
Compact: from 135 mm x 75 mm x 96 mm
Thanks to these product features, the additional load on the robot is minimized and it is easier to integrate imaging.
Advantages of the Stereo visard camera for robotic arms
The Stereo visard camera is the perfect solution for applications where robots need to work with a state-of-the-art camera system. It offers:
Autonomous data processing & Real-time capability:
Thanks to on-board processing, the camera can process image data without external computing resources to interact quickly with the robot arm.
Precise 3D capture:
Ideal for applications such as bin picking, it detects objects in 3D and calculates their exact positions.
Robust design:
Well-suited for industrial use and dynamic applications, such as robotic arms.
Simple integration:
With an Ethernet connection and software interfaces, the camera can be easily integrated into robot systems. Hand-eye calibration is ensured via REST API interface and ensures easy adaptation to the respective robot system.
Basler Application Software for Robotics
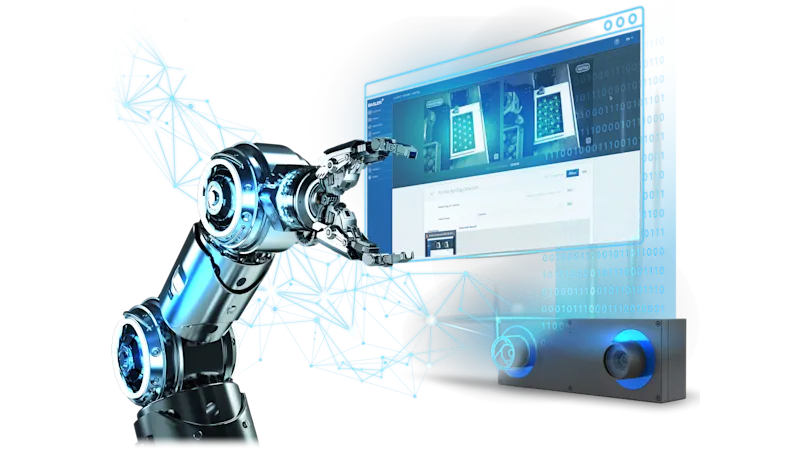
The individual software modules are made for typical robotics applications such as object recognition, picking tasks and navigation. They can be activated for the respective application via plug-and-play and operated intuitively, keeping your overall system costs low.
Application Software for Robotics