Additive Manufacturing: Limited Space Meets High Performance Requirements
When manufacturing and repairing components, additive manufacturing is often used for layered material application, similar to 3D printing. Process monitoring and quality assurance are performed by imaging systems, with the choice of vision system determined both by the limited space available and the high performance requirements.
Machine vision monitors process quality
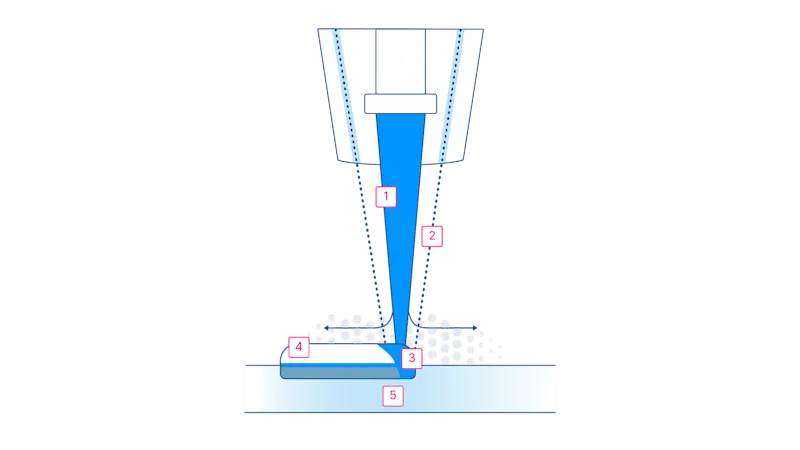
Additive manufacturing refers to combining materials for the generative buildup of components (often made of metal or plastic) from 3D model data, usually layer by layer. Optical inspection is essential to ensure the quality of such components.
In the production of metallic components using laser metal deposition, for example, a powder is introduced into a laser beam via a powder nozzle, which melts it with pinpoint accuracy in the melt pool and applies it precisely. Here, machine vision monitors the ongoing process.
Variable camera solution for lack of space
Melt pool monitoring places two requirements on the image processing system: very little available space and a high data rate for real-time monitoring. The modular dart M board level camera with GigE interface is therefore well suited for this application.
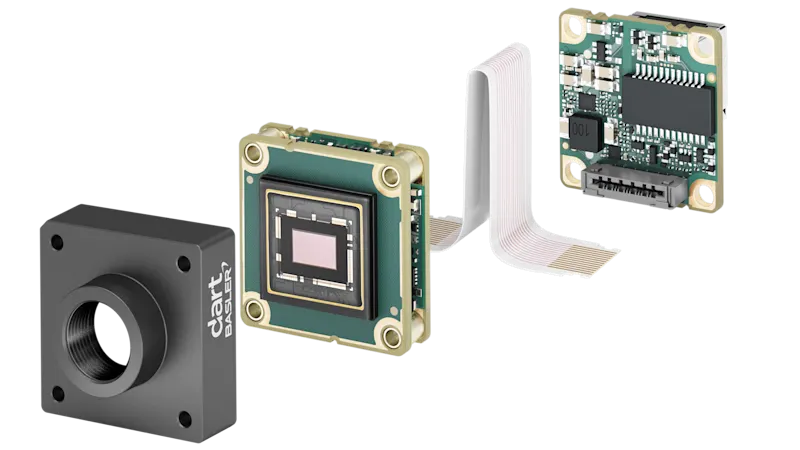
At its heart is the small 27 mm x 27 mm camera module, which is equipped with the Sony Pregius IMX287 sensor and achieves a frame rate of 290 fps at VGA resolution. It is connected to the interface board via a 15 cm long flat flex cable. The cable allows the camera module and interface board to be physically separated from each other in order to save space at the image acquisition location, i.e. the melt pool. It also allows flexible alignment of the interface board for easier integration.
The board features a GigE standard RJ45 connector and PoE (PoE over Ethernet), enabling a simple, single-cable connection between the camera and host system. The GigE interface in turn allows long cables (up to 100 m) to the host system for spatial separation from the camera. In the case of melt pool monitoring, an S-mount lens and matching lens mount are also required. At 29 mm x 29 mm and a weight of 15 g, the camera module with S-mount still easily meets the requirements of being small and light.
Modular design of the dart M
The dart M camera adapts to the installation environment of the application: beginning with the camera module, the appropriate camera is configured on a modular basis.
Advantages of the dart M for additive manufacturing
Using this modular GigE camera and its real-time image output, it is possible to monitor production, search for errors, and adjust process parameters during operation. Only one part of the camera can be placed in the building area, saving valuable space. In-house electronics can be combined with the camera components so that only the necessary components need to be purchased, allowing you to optimize costs.
Flexible dart M cameras feature individually available components to suit the application, existing electronics, and installation situation
Simple and fast hardware integration using the pylon Software Suite with drivers and APIs for GigE vision systems
High GigE data rate for real-time images
Perfect for other application fields, including factory automation, logistics, robotics, medical technology, and electronics inspection - also with multi-camera setups thanks to the GigE interface
Products for this solution
Looking to implement a comparable solution? These products will help you.