Introducing an Advanced Solution for Long Exposure Imaging: Addressing Thermal Noise and Hot Pixels
Long exposure imaging is essential for detecting subtle defects (such as dead pixels in displays or faint signals in semiconductor inspection) under low light. However, long exposure times often introduce challenges like hot pixels.
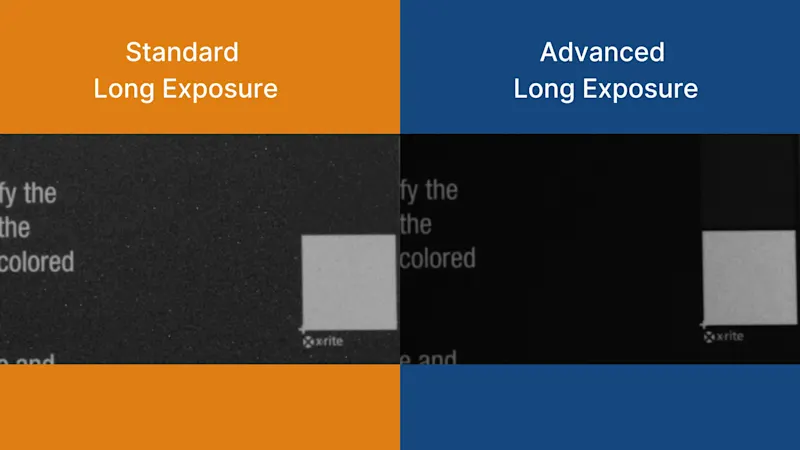
Capturing every detail with long exposure times
In both display and semiconductor inspections, precision is paramount and every tiny detail matters. In display inspections, long exposure is often used to detect low-luminance defects and color uniformity variations. In semiconductor inspections, while short exposure times are preferred for high throughput, long exposure plays a crucial role when light levels are too low to generate a signal distinguishable from noise.
Key challenges in long-exposure imaging for semiconductor and display inspection
Longer exposure times introduce challenges such as increased thermal noise, hot pixels, dark current, and motion artifacts, all of which can degrade image quality and compromise inspection accuracy.
Thermal noise and hot pixels:
Longer exposure times cause sensor heat buildup, generating thermal noise and hot pixels that mimic defects, leading to false positives and costly rework.
Image detail loss:
Motion artifacts from mechanical shifts, environmental vibrations, or thermal expansion blur fine details in high-magnification semiconductor imaging and high-resolution display analysis.
Signal-to-Noise Ratio (SNR) trade-off:
While longer exposure times improve SNR by capturing more photons, they also amplify hot pixels and dark current noise, masking critical defects in high-resolution sensors.
Cost vs. image quality:
High-end sensors with optimized cooling minimize noise but increase cost and complexity, making them impractical for budget-sensitive applications.
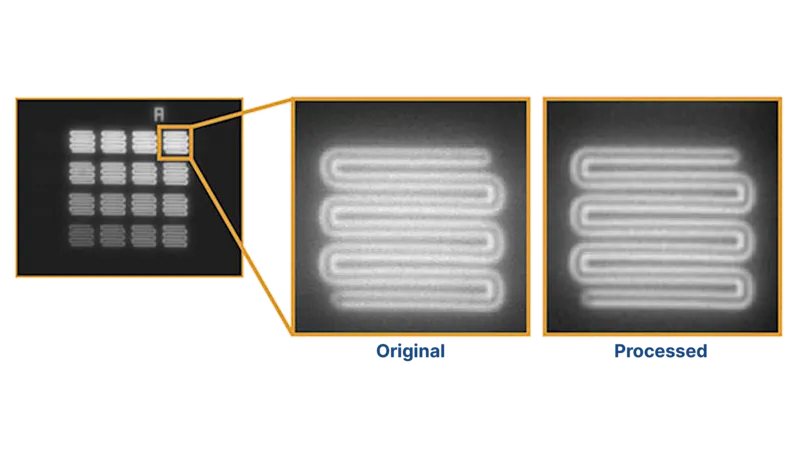
Different ways of addressing thermal noise and hot pixels
To overcome these challenges, a combination of sensor optimizations, cooling solutions, and advanced image processing techniques can help maintain precision without sacrificing efficiency.
Method | How It Works | Pros | Cons |
---|---|---|---|
Hot Pixel Correction | Identifies and corrects hot pixels over multiple frames. | Directly targets hot pixels, preserving signal integrity. | Computationally expensive for real-time applications. |
Traditional Dark Frame Subtraction | Captures a dark reference image and subtracts thermal noise from the image. | Effective for static noise patterns. | Requires two frames and cannot handle time-varying noise. |
Pixel Mapping & Masking | Identifies and replaces hot pixels with neighboring pixel values. | Effective for persistent hot pixels. | Can distort real defect patterns. |
Temporal Noise Reduction (Frame Stacking) | Averages multiple frames to reduce random noise | Improves SNR, works well for static noises. | Not suitable for moving objects or dynamic scenes. |
Optimized Camera Housing Design | Reduce sensor temperature to prevent thermal noise and hot pixel generation. | Prevents hot pixels at the source, enhancing image quality. | Does not eliminate all noise, especially in extremely long exposures. |
The best approach: a hybrid solution
For optimal image results, especially in complex environments like semiconductor and display inspection, there is no standard solution that solves all the problems. Thus, a hybrid approach is recommended. For example, combining both hardware solutions and post-processing algorithms.
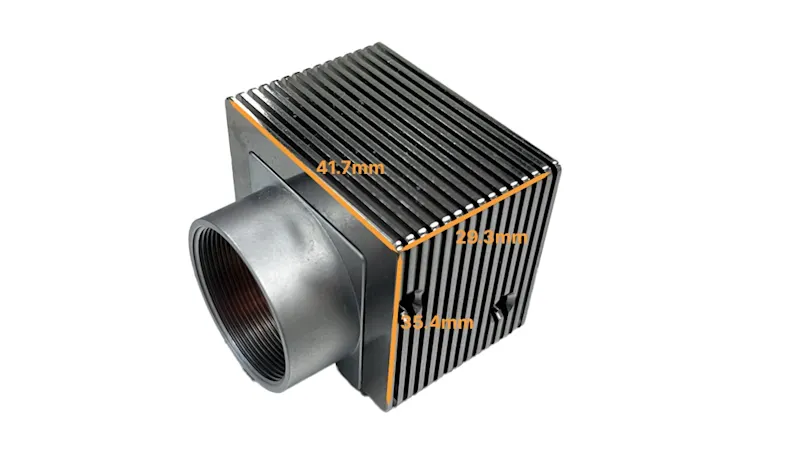
Hardware-based optimization: A well-designed camera housing that keeps the sensor at a stable, low temperature can significantly reduce the generation of thermal noise and hot pixels. Keeping the camera core temperature below 45°C is especially effective in minimizing hot pixels.
Software-based post-processing: Post-capture, algorithms such as hot pixel correlation, dark frame subtraction, and pixel mapping can refine the image, correcting any remaining artifacts caused by long exposure.
Real-time FPGA-based noise reduction: Advanced FPGA-based solutions can dynamically adjust exposure settings and perform real-time noise correction directly at the sensor level, ensuring noise and hot pixels are minimized without adding processing delays.
There’s no single fixed solution—it must adapt to changing application needs. Our job is to thoroughly understand the application and quickly find the best balance between cost and performance. In our lab, we push solutions to the limit, and when we provide a test image from a 15-minute exposure, customers are thrilled with the results.
Results: maximizing long exposure imaging performance
Benefit from our advanced solutions for both semiconductor and display inspections that effectively tackle the challenges of long exposure imaging.
Reduced Hot Pixels: Our dynamic hot pixel correction algorithm keeps hot pixels below 2 ppm (pixel per million) at 8 sec exposure time with 27dB gain setting, ensuring clearer defect detection.
Real-time with 0 CPU loading: Running multiple image processing algorithms directly on the camera’s FPGA—instead of on your PC—ensures high-quality results with zero CPU load, enhancing efficiency.
Optimized Exposure Settings: Whether for dynamic display inspection or high-precision semiconductor analysis, we provide optimized exposure settings that adapt to your inspection needs.
Compact and Efficient Cooling Solutions: Prevent the generation of hot pixels in the first place with our optional cooling design, which complements post-processing efforts for even better results.
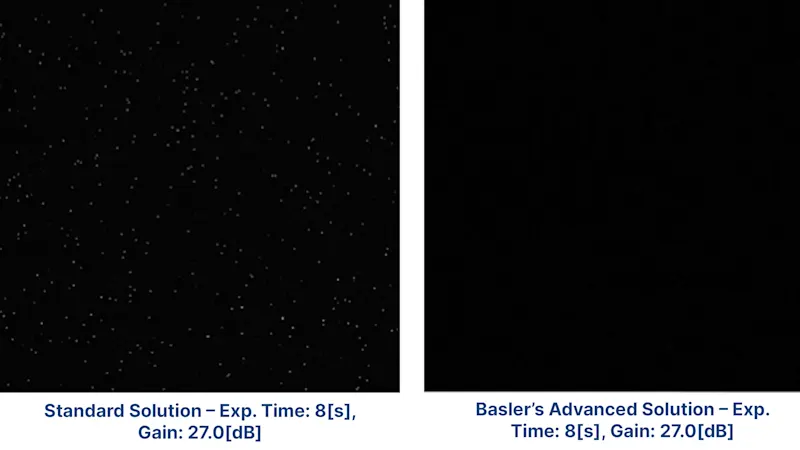
With Basler’s hybrid approach and dynamic solutions, you achieve superior imaging performance, enhanced inspection accuracy, uncompromised processing speed, and cost efficiency—empowering you to get the best results.
Test it or try it—contact our engineersProducts for this solution
Looking to implement a comparable solution? These products will help you.