Image Processing in Battery Cell Manufacturing
Machine vision provides quality control
In the production of battery cells, ensuring high quality during all process steps and reducing material waste are crucial. Digital image processing enables the reliable detection of even the smallest defects. Our solutions help produce safe, high-quality battery cells to meet the challenges of electric mobility.
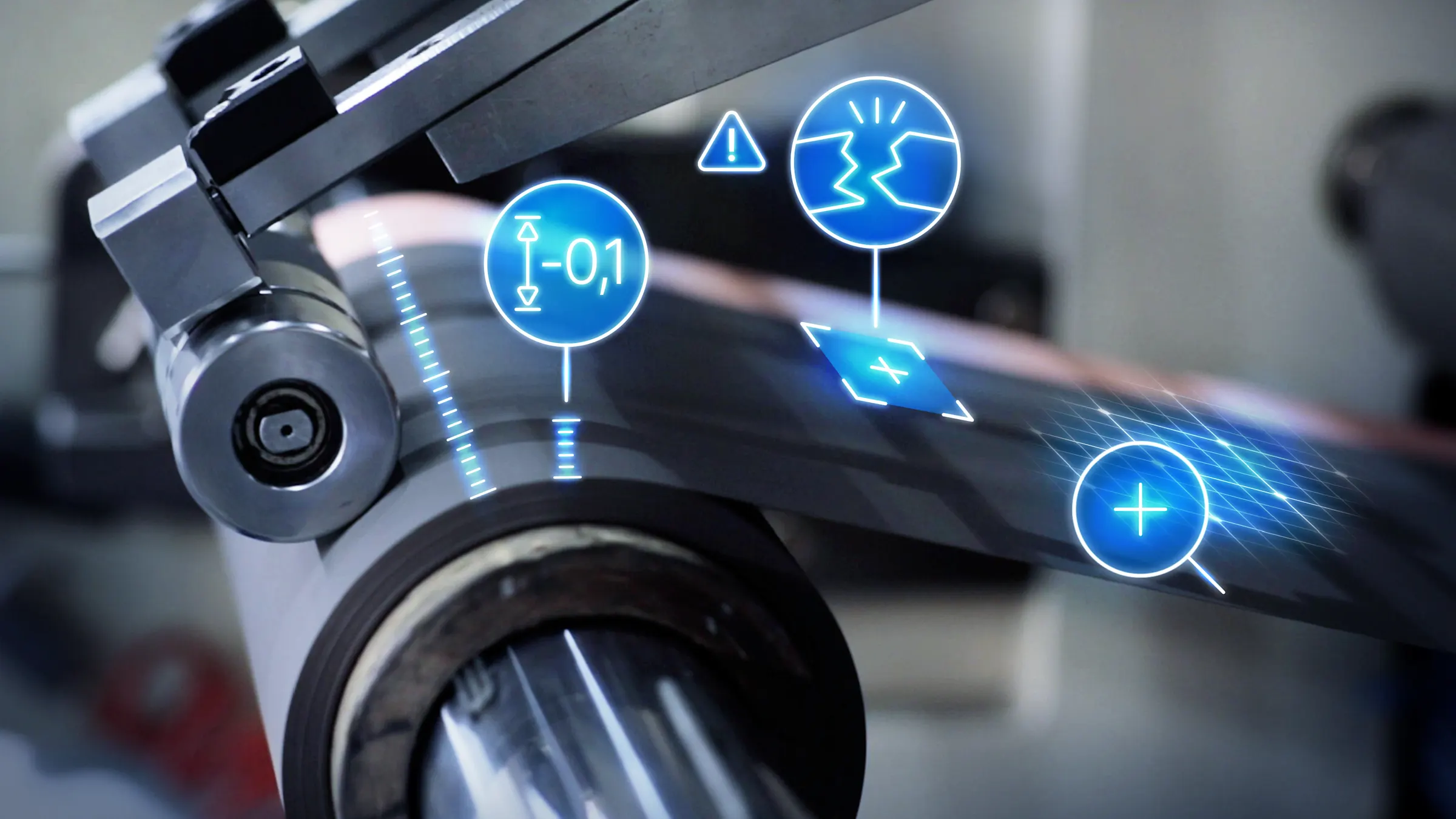
High performance & speed
Innovative, high-performance camera technology for state-of-the-art production methodsDurable & reliable
With the lowest failure rate in the industry, our camera systems stand for reliability in 24/7 operationSimple integration
All of our components are compatible and easy to connect to target systems using pylon softwareAvailability & reliable delivery
Stable supply chains ensure long-term availability of our products and prevent production downtime
Efficient quality control in battery cell production
Find out in our webinar:
How machine vision is used for quality control in the production of battery cells
More about typical machine vision applications in battery cell production
How you can increase the efficiency of your production by using machine vision
Different cell types
The main application for lithium-ion battery packs is electric mobility. Though there are three types and formats in use, the functional principle of all types is essentially the same. The main differences are in the design, requirements, and materials used.
Battery cell manufacturing involves four main process steps
Lithium-ion battery cell production consists of four main process steps: electrode production, cell assembly, cell finishing, and battery pack assembly. The electrode production and cell finishing process steps are largely independent of the battery cell type, while cell assembly distinguishes between pouch or prismatic cells and cylindrical cells. Regardless of the cell type, the smallest unit of any lithium-ion cell consists of two electrodes and the separator that divides them from one another. In between is the ion-conducting electrolyte.
Machine vision ensures product quality and process stability
Machine vision systems provide valuable information during the production process, including inspecting materials and ensuring process steps are correctly executed. Different solutions are available depending on your application needs. By combining our frame grabber-based systems with VisualApplets and our high-sensitivity line scan cameras, the resulting vision system can easily cope with the high speeds found in electrode production. High-resolution ace 2 X visSWIR cameras inspect the structures of separator foils inside the cell. Our area scan cameras, working in conjunction with pylon vTools, check that the cathode and anode are correctly positioned on top of each other during the winding of prismatic cells. Catching even the smallest defect is critical, since accurate error tracking increases productivity.
Where is vision used in battery cell manufacturing?
Use cases in battery cell manufacturing
Machine vision helps ensure the quality of processed materials and minimizes possible material waste. Our solutions can help.
Most popular products
For efficient and reliable machine vision applications in this industry, the following Basler products are often the best choice: