Machine Vision Solution for AI-Supported Gripping of Flexible Packaging
Automated handling of different bags
Flexible packaging, such as pouches and bags, play a central role in modern intralogistics. From foil bags in the food industry to plastic bags for raw materials to shipping bags in e-commerce – the variety of bags place high demands on automated handling systems. With a vision solution consisting of a 3D camera and special software, the various bags can be handled reliably.
All challenges under control: Innovative gripping technology for flexible packaging
Flexible packaging, such as pouches and bags, can quickly push conventional gripping systems to their limits. Varying shapes, fill levels, and materials – such as thin, reflective, or transparent films – all make secure gripping more difficult. However, with the 3D Application Software for Robotics module ItemPickAI, a wide variety of "bags" can be handled reliably: from transparent bags to those with deformable contents to paper bags. Thanks to customizable parameters, gripping even stacked or overlapping packages is ensured.
AI and 3D technology combined for optimal gripping results
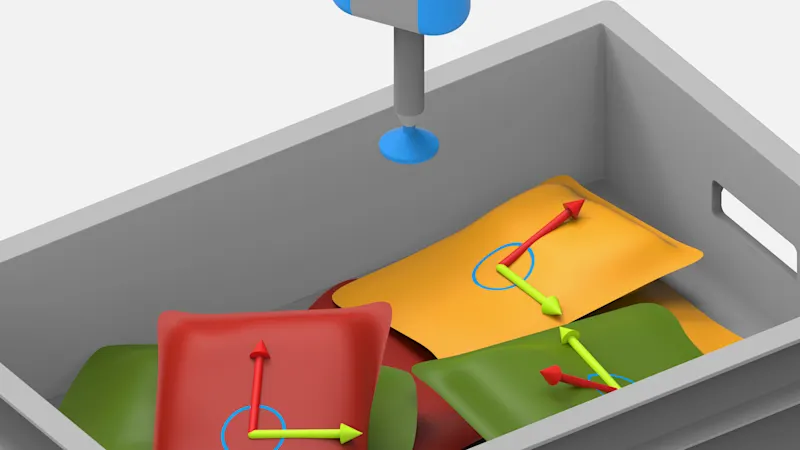
ItemPickAI software for AI-based gripping
Our AI software ItemPickAI is based on a neural network. For robot-assisted pick-and-place applications with suction cups, it calculates precise gripping positions for flexible, previously "unseen" objects of a defined category – even if they are delivered in unstructured containers or load carriers. Both single-type and mixed configurations can be implemented without any problems.
To set it up, all you have to do is specify the object category (e.g. "Bags") and the suction surface size of the gripper. These parameters can be flexibly adjusted. In this way, processes such as pickingand (de-)palletizing can be implemented quickly and efficiently – without expert knowledge in AI or image processing.
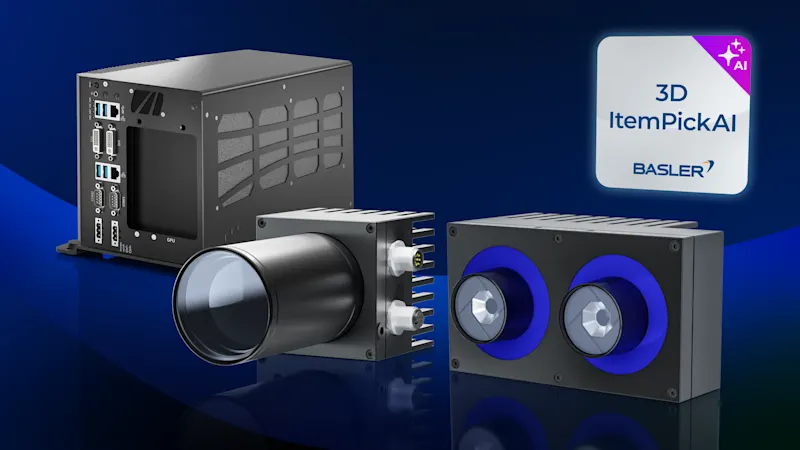
Hardware components of the 3D robot system
Stereo Camera & 3D Camera Cube: Basler's Stereo visard or Stereo ace cameras enable precise depth detection of the recorded scene. They can be set up either on-arm directly on the robot or off-arm statically. The pre-installed onboard firmware of the Stereo visard allows plug-and-play commissioning. In combination with the 3D Camera Cube, the required power is provided for the software modules, such as ItemPickAI, for individual robotics applications.
3D Accessories: For even more reliable image acquisition, the system can be expanded with a Stereo Camera Randomdot projector and optimized with additional lighting.
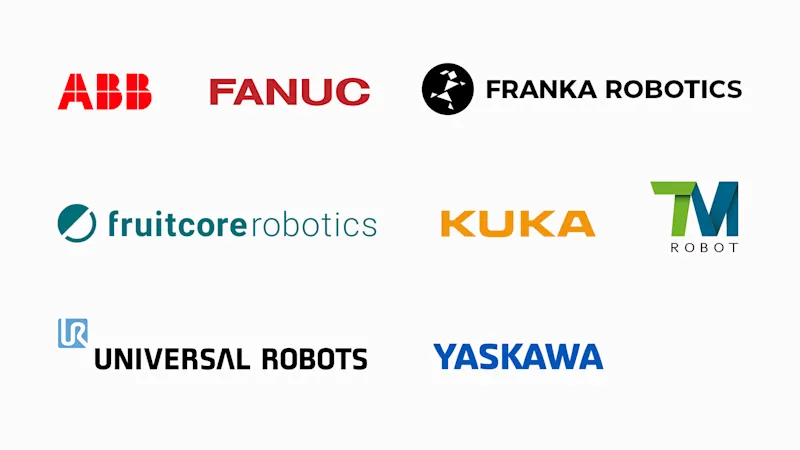
Robot Integration
Efficient handling requires a suitable robot, the right gripper, and a seamless interface. Depending on the application, vacuum or mechanical grippers are used. We offer various solutions so you can easily use our 3D cameras and software modules with your favorite robots. Thanks to software interfaces, our products are compatible with robots from ABB, Fanuc, KUKA, Universal Robots, Yaskawa, Techman Robot, fruitcore robotics and Franka Robotics.
Is your robot not listed? We will find a way to support you!
Contact usTechnological advantages and added value
High-resolution 3D images: Thanks to active stereo vision, the system also captures difficult surfaces, including shiny or transparent materials.
Precise decisions thanks to AI: Powerful neural networks calculate gripping points based on image recordings within about 1/4 second.
Real-time object detection: Due to the camera's onboard image processing and the AI-supported analysis, the calculation of gripping points takes 1/4 second. This easily enables over 1000 picking operations per hour.
Robust gripping of flexible objects: The system automatically adapts to different bag and bag variants without the need for time-consuming reparameterizations.
Easy integration: ItemPickAI is configured and read via the standard interface of the Camera Cube, which includes the integrated WebGUI, REST API, OPC UA, ROS and our software interfaces.
Increased efficiency and scalability: Automation reduces manual intervention, increases throughput, and improves sorting accuracy. This accelerates the return on investment.
Products for this solution
Looking to implement a comparable solution? These products will help you.