What Role Does Computer Vision Play for Industry 4.0?
Under the umbrella of information technology, computer vision plays an essential role. Machine vision is an indispensable component of every automated environment. This is true for hardware - such as in robotics - and in software for image analysis purposes or for training artificial neural networks (Deep Learning).
What contribution does computer vision make? Let's take a closer look at the example of a Smart Factory.
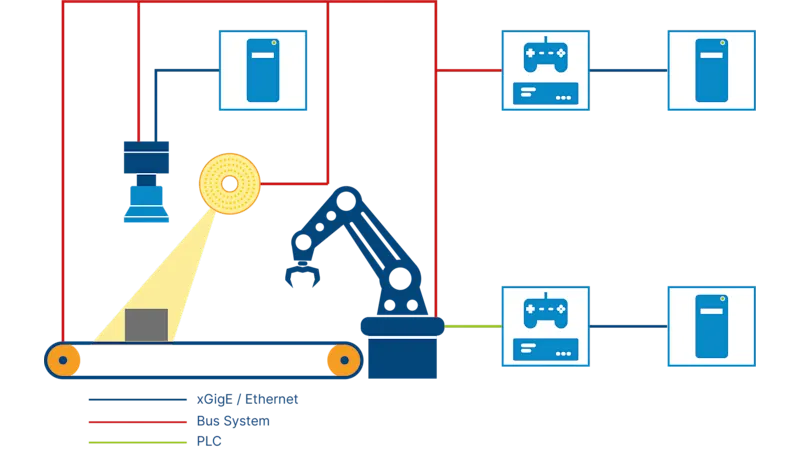
What is so smart about the Smart Factory?
The term Smart Factory describes the intelligent networking in the field of factory automation. Knowledge, consisting of data and processes, is a fundamental prerequisite for an intelligent factory. Where does this knowledge come from?
Data is usually collected with the help of sensors. However, without appropriate processing, the data from the sensors is worthless; it must be made usable for several systems and components so that it can serve as a basis for decisions in processes. This is exactly where the factory becomes smart.
The secret lies in the networking of all individual or sub-systems involved. The basis of their networking is usually a so-called bus system, which connects all sensors and actuators via the same data lines both with each other and with an automation device, for example a control system (PLC).
Since the subsystems and devices in a factory are sometimes located far away from each other, the bus systems are usually based on real-time Ethernet. The Ethernet standard is widely used, hardware accessories such as cables or switches are available at low cost, and long cable lengths between the individual systems can be implemented without problems.
Vision systems as data suppliers
Among the most important and powerful sensors in an automated factory environment are vision systems with cameras. They already play an extremely important role in modern automation and usually consist of the following components:
Networking in a factory setup with OPC UA
Like all other subsystems, the vision system must be connected to all other systems and to the central control system, both in terms of hardware and software. This is done by means of special data exchange standards for industrial communication. These standards give the individual subsystems a common machine language, so to speak, to ensure easy interoperability between them. One of these standards is umati (universal machine technology interface). It uses OPC UA as an open, universal interface standard.
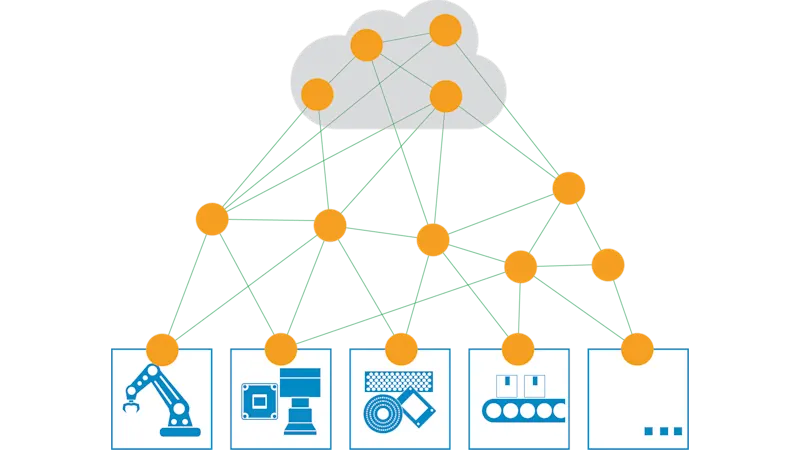
OPC UA makes machine data machine-readable and semantically writable. The standard provides for the preparation of e.g. sensor data and control commands, defines their transport and determines the interfaces between systems and security mechanisms.
The standard can be used at all levels of a factory setup: from the lowest field level, where the sensors and actuators are located, to the abstract information layers such as SCADA (Supervisory Control and Data Acquisition), ERP (Enterprise Resource Planning) or the cloud.

With the help of OPC UA, the different components can be networked horizontally on one level as well as vertically across the different levels.
Real-time capability is indispensable for efficient use in all areas of an intelligent factory. For this purpose, the standard offers expansion options in the form of TSN (Time Sensitive Networking). OPC UA TSN is also a prerequisite for transmitting images directly from the vision system to the other subsystems or to the control unit - a functionality that has not yet been implemented.
Smart Factory made easy
The central interface of the systems is a PLC, which now contains all subsystems and their software. This central node is also the interface to the higher-level systems such as the ERP. The structure could be further reduced by outsourcing higher-level systems to the cloud.
In such a setup it would be possible to easily connect both the conveyor belt and the robot as well as the individual components of the vision system. With their PTP, the cameras already provide the basis for real-time capability when OPC UA is used as standard and possible extensions such as TSN are available.